The crucial step in applying shrink sleeve labels to your product container is using an appropriate shrink tunnel. Selecting the right shrink tunnel is essential to achieve the best final appearance, so knowing how to choose the correct tunnel is essential. Shrink tunnels come in various types, each with unique benefits. The primary ones include Electric heat shrink tunnels and Steam shrink tunnels. Sometimes a mixture of heat types, like steam shrink tunnels with electric heating zones, might be selected. We posted this article to help you identify the best tunnel type for your product’s container.
Understanding Shrink Films
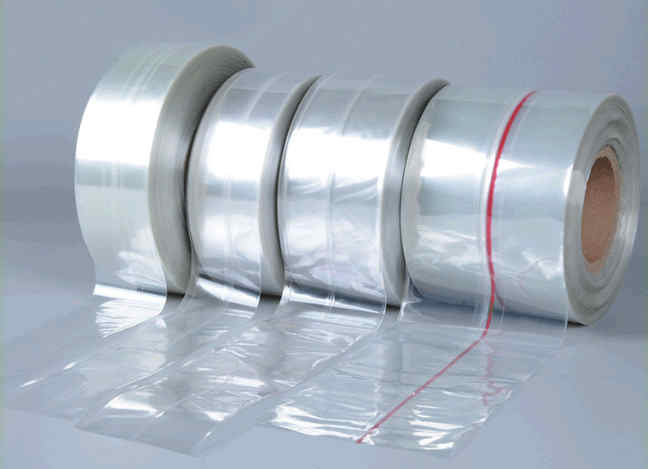
Before choosing suitable shrink tunnels, we need to learn more about shrink films. Shrink films are primarily made from polymer plastic film, the most common of which are PVC, PETG, OPS, and PLA. Each of these materials has strengths and weaknesses, and selecting between them depends on the product’s specific requirements to be labeled.
One of the critical factors of shrink films in choosing a shrink tunnel is the percentage of shrink required for your product’s container. Typical shrink percentages are up to 55%, while some containers need a high shrink up to 65-70%. These require different shrink films and a high-precision tunnel for superior results. Determining and using a suitable film grade is vital to the success of your project. Choosing the wrong film for your labels could result in expensive production time, wasted materials, and potential loss of products.
Electric Heat Shrink Tunnel–Dry Heat Tunnels
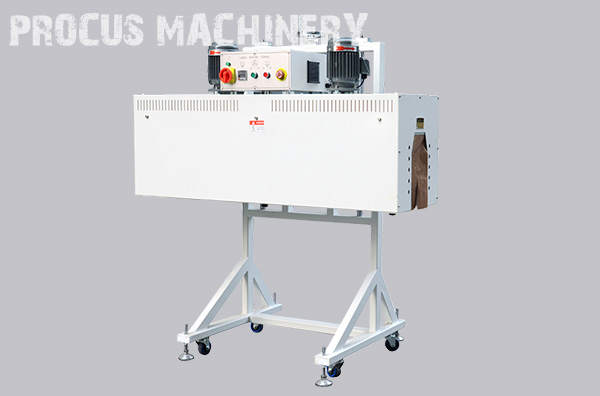
Some products that require a dry labeling environment or sterile environment suit the dry heat shrink tunnels. However, controlling shrink films in dry heat is challenging. They can shrink rapidly and are more distorted than steam shrink tunnels. But Preheating containers might improve shrinking quality in electric heat shrink tunnels.
— Issues with Pigment Concentration
A downside of dry hot air tunnels is the uneven shrinkage of the sleeve in parts, leading to pigment concentration. Steam tunnels prevent this issue by ensuring even and accumulative shrinking.
— Effects on Empty Plastic Bottles
Electric heat shrink tunnels can distort or melt empty plastic bottles due to high operational temperatures.
Therefore, when we use the electric heat shrink tunnel, we must pay special attention to formulating the shrink tunnel plan. It is necessary to comprehensively consider the relationship between the product container, production speed, shrinkage temperature, and tunnel length and find the most suitable solution so that the product can achieve a perfect shrinkage effect when it passes through the electric shrink tunnel.
Steam Shrink Tunnels
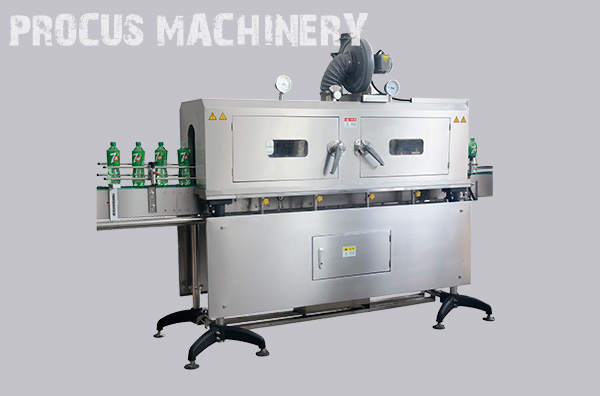
Steam shrink tunnels are the most versatile and practical for shrinking full-body sleeve labels. They provide high-quality shrink results on complex containers like an oval, hourglass, tapered, and offset neck shapes. They are suitable for full and empty containers and cold-filled packages.
Steam is more efficient at transferring heat than dry heat. Steam shrink tunnels usually run at 175 – 200 degrees F, while dry heat tunnels must operate at 350 – 500 degrees F to get similar results. Steam is also accommodating as a single setting of a steam tunnel can often be used for all label colors, while dry heat tunnels may need adjustment again for various colors.
— Disadvantages of Using Steam
A stable steam supply at a moderate pressure is necessary, which may require in-plant steam, or the installation of a steam boiler, typically 48 to 174 KW (4.8 to 17.4 HP) in size. Boilers can be powered by electricity or natural gas. Consider the boiler cost and professional installation by a licensed plumbing company. With steam tunnels, the product will have minimal moisture vapor or droplets upon exiting the tunnel, which typically evaporates quickly. Sometimes, companies add air knives to dry the containers once they go through the steam tunnel.
Dual Zone/Multi-Zone Tunnels
For an optimal shrink process and an attractive product, it’s common to use dual-zone, multiple tunnels, or multi-zone tunnels for shrink label applications. In high-speed operations, two or more tunnels, either the same or different types, might be used sequentially. A pre-shrunk or post-shrink heater unit can be combined with the tunnels for special applications. Using multiple zones allows for targeted heating at specific package points, with varying temperatures, to achieve the desired effect.
Usually, the first zone focuses on the package base to secure the label under a bottom radius to prevent lifting. Secondary zones target the package body and critical graphic areas. Final zones, often multiple, can concentrate on the neck area, where the highest shrink percentage is typically needed, like on wine, beer, or trigger spray bottles.
Testing is Essential
Ensure future shrink tunnel suppliers conduct tests and provide samples and a video. This will necessitate you to provide containers, caps, and sleeves from your selected material supplier. Although it involves some effort, it assures that the tunnel you buy will yield the desired result once installed in your facility.
In Summary
Selecting the right shrink tunnel is critical in applying shrink sleeve labels to your product. The type of shrink tunnel depends on the required shrink percentage and involves choosing between dry heat tunnels, dual/multi-zone tunnels, and steam tunnels. Each type has advantages and challenges; sometimes, a combination can be beneficial. It’s essential to understand the nature of your product, the shrink film required, and other factors such as package shape and material. A crucial part of the process is conducting thorough tests with potential suppliers to ensure the tunnel will deliver the desired results once installed in your facility.