Are you facing difficulties with your Shrink Sleeve Labeling Machine or Shrink Tunnel? You’re not alone, and we have the solutions you need. From common problems like material accumulation on the mandrel to uneven cuts on shrink sleeves, our comprehensive guide delves into the underlying causes and offers practical solutions to get your operation back on track. Whether you’re dealing with irregular bottles, frequent jams, or cutter misalignments, we’ve covered many issues and remedies that cater to different machine designs and bottle shapes. Before seeking professional help, take a moment to explore this guide – the answer to your problem may be just a scroll away.
Feel free to modify or use this as you see fit!
Shrink film accumulates material (jam) on the mandrel.
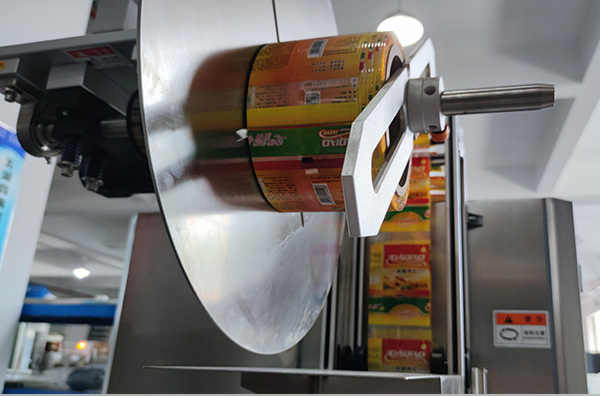
Causes:
(i) This is because the control of the shrink film’s folding diameter during manufacturing is either too large or too small. It’s more prone to material accumulation on the mandrel, especially when it’s below the standard size (too small).
(ii) Using a single point for clamping the mandrel can easily lead to instability in holding, which makes it difficult for the mandrel to remain straight, leading to material accumulation.
(iii) Adjusting the upper and lower rubber driving wheels might be inconsistent.
(iv) Whenever the cutting blade completes a rotation and returns to its starting point, it might stop in the wrong position. This situation causes the shrink sleeve labels to touch the blade, accumulating material.
(v) The grooves in the mandrel might have been “cut” or “scratched” by the blade, causing the labels not to move smoothly.
(vi) After the label has been cut while waiting to be brushed off, the brush-off wheel might not accurately and smoothly apply the cut label to the bottle, leading to a domino effect where the label reflects, and causes shrink sleeves accumulation on the mandrel.
Solutions
(i) Label suppliers should maintain the folded diameter within ±0.5% of the standard value.
(ii) Opt for machines with multi-point clamping, superior to single-point clamping. But Different sleeve labeling machines may have various designs, so careful consideration is needed when purchasing.
(iii) Properly adjust the upper and lower rubber driving wheels.
(iv) Check the blades’ return position for accuracy. Ensure that the next label is driven after the blade leaves the mandrel. Blades should stay within the blade holder and not approach the mandrel grooves to ensure no accumulation of material.
(v) If the mandrel groove shows signs of damage, smooth its surface before use.
(vi) Ensure that the brush wheel and mandrel’s clamping touching is accurate and that the brush wheel isn’t worn out. This situation ensures labels slide onto bottles without causing accumulation on the mandrel.
Uneven Cuts on Shrink Sleeve, Resulting in Rough Edges:

Causes:
Most of the current market’s sleeve labeling cutters are cut with a design where multiple blades overlap at the cutting point, leading to difficult-to-eliminate rough edges. However, the main reasons causing significant rough edges are:
1. The sleeve label is too large, with a significant deviation between the diameter of the mandrel and the folded diameter of the shrink sleeve film.
2. The cutter wheel’s calibration points are not on a horizontal line.
3. Within the cutter wheel assembly, the gap between the mandrel groove and the bottom of the knife holder is too large, causing the blade to be uneven.
4. The cutting force of the blade needs to be increased.
Solutions:
1. Control the label size and ensure the fold diameter matches the mandrel diameter.
2. After replacing the blade, ensure all blade leveling points are horizontal and appropriately tighten the blade.
3. Replace the relevant parts within the cutter wheel assembly.
4. Replace with a new blade.
The blade easily cuts into the center column, causing the blade to break.

Causes:
1. The mandrel may not be correctly installed. If it’s not securely clamped, the mandrel might slide down during the sleeving process, causing the blade to cut into it and break.
2. The blade may not be securely locked, leading to slipping during operation and consequent breakage.
Solutions:
1. Install the mandrel correctly. Opting for a multi-point clamping design can effectively prevent this issue.
2. Regularly check the screws within the cutter wheel assembly, such as the bottom of the knife holder, the knife holder itself, and the cover plate.
For irregular bottles, the temperature of the shrink tunnel frequently needs to be adjusted.

Causes:
1. Irregular bottles, by their nature, have an inconsistent shape. When the shrink film encounters heat, it shrinks. The irregular shape of the bottle, with varying diameters and forms, requires adjusting the shrink tunnel temperature.
2. It might be due to unstable steam pressure provided by the client.
3. The shrinkage rate of the shrink film may be inconsistent.
4. Whether the production speed is constant? And if the conveyor belt speed often changes?
Solutions:
1. To achieve perfect shrinkage and effectively control the curving shrinkage of irregular bottles, it’s necessary to adjust the blowing port’s appropriate position inside the shrink furnace. Depending on the bottle’s various features, give hard-to-shrink parts of the bottle adequate shrinkage time and temperature.
2. Use a high-quality pressure-reducing valve or an imported one.
3. Ask the label supplier to provide labels with a stable shrinkage rate.
4. Conveyor belt speed should be set based on the maximum production capacity. Once the rate is set, it’s advised not to adjust it frequently.
Suggestion:
Due to the market’s wide variety of irregular bottles, a single sleeve labeling machine is hard-pressed to meet all bottle shapes. Hence, before purchasing a shrink labeling machine and shrink tunnel, customers should have thorough pre-production communication with manufacturers. This ensures that the equipment supplier considers all the bottle shapes the customer requires. Doing so guarantees the machine’s compatibility with all the client’s bottle types during usage.
Common Problems of Shrink Sleeve Label Applicator:
Frequent sleeve label jams in the feeding and shrink film overlap:
Solutions:
1. Ensure the shrink sleeve does not have joint parts.
2. Address the gap issue between feed wheels.
3. Clean excess dust on the feed wheel.
4. Avoid too fast feed speed.
5. Ensure the shrink film between the feed wheel and mandrel is aligned.
Many labels fail to cover the bottom of the bottle during sleeving:
Solutions:
1. Ensure bottles aren’t overly damp.
2. Use more label brushes.
3. Ensure the brushing wheel isn’t dropping to the base of the mandrel, causing labels to lose their circular shape.
4. Adjust the brush wheel tightness to avoid label deformation.
Frequent sleeve label jams on the mandrel:
Solutions:
1. Check label size and ensure label joints are correctly connected.
2. Adjust the gap between the drive wheels.
3. Make sure the leaf springs aren’t too open.
4. Correctly set the cutter’s original position.
Many labels fail to fit on the bottle during sleeving:
Solutions:
1. Ensure the bottle and mandrel are aligned.
2. Secure the mandrel properly to prevent shaking when the machine starts.
3. Adjust the sensor position for bottle detection.
Multiple labels are dispatched continuously for a single bottle detected by the sensor:
Solutions:
1. Check if the label size is too large.
2. Adjust the brushing wheel’s height to prevent repeated brushing of labels.
The machine’s performance declines after attaching a new shrink film:
Solutions:
1. Assess label quality changes like size, thickness, and shrinkage rate.
2. Ensure an operator properly attaches the newly connected shrink film to prevent breakage or jams on the mandrel.
The machine frequently misplaces the cut position:
Solutions:
1. Clean the dirty segment sensor.
2. Adjust the sensor’s sensitivity.
3. Properly adjust the touchscreen parameters.
4. Check for loose drive belts.
The machine’s cutter damages easily:
Solutions:
1. Properly set the cutter’s original position.
2. Secure the mandrel’s drive wheel.
3. Stop the machine immediately during a jam.
4. Clean any residual labels in the cutter after a jam.
5. Ensure the cutter blade is correctly installed.
The labeling machine jams when there’s a thickness variation in every roll of shrink film:
Solutions:
1. Ensure the thickness of the shrink film is within the specified range to avoid jams.
The bearings and metal pieces at the base of the machine’s mandrel wear out quickly, affecting sleeving quality:
Solutions:
1. Adjust the brushing wheel’s tightness to prevent long-term wear and tear on the bearings and metal pieces.
The spring casting position that secures the cutter often shifts, making the cutter misaligned, leading to excessive debris and jams:
Solutions:
1. After aligning the cutter horizontally, tighten the screws on the cutter to maintain its position.
Note:
1. The above causes and solutions are for reference only. For actual problems, consult your supplier. Remember, each machine and situation may have unique challenges, so it’s crucial to understand the specific requirements and consult with experts when needed.
2. To ensure that the functions of each part of the machine are fully utilized and to improve production efficiency, please ensure timely maintenance.