Shrink tunnel machines have become an essential tool in many industries today. These shrink tunnel machines have several variations, each with distinct features and applications. Among these tunnels, the electric heat shrink tunnel stands out. It has become one of the vital heat shrink tunnels used in various packaging processes, particularly with products that require shrink sleeve labels.
What is an electric heat shrink tunnel?
An electric heat shrink tunnel is one of the shrink tunnel machines used in packaging. Electric heat shrink tunnels utilizes electric heating elements to create a controlled and consistent heating temperature to shrink film, such as PVC, PETG, OPS, and PLA, to apply heat to shrinkable materials wrapped around products, effectively sealing and securing the packaging. An electric heat shrink tunnel is also called a hot air shrink tunnel or heat shrink tunnel machine.
How does an electric heat shrink tunnel work?
An electric heat shrink tunnel uses heating elements to generate hot air, and then blowers circulate the hot air around the package with the shrink sleeve. As the hot air contacts the shrink material, it causes it to contract or “shrink” around the product, forming a tight and secure wrap. The blower ensures the heat is evenly distributed throughout the tunnel, allowing for uniform shrinkage and a polished final appearance.
What’s the inside temperature when an electric shrink tunnel is working?
The temperature inside an electric shrink tunnel can vary widely, counting on the specific requirements of the shrink film being used and the product being packaged. Generally, the temperature can range from as low as 50°C (122°F) to as high as 200°C (392°F) or even more.
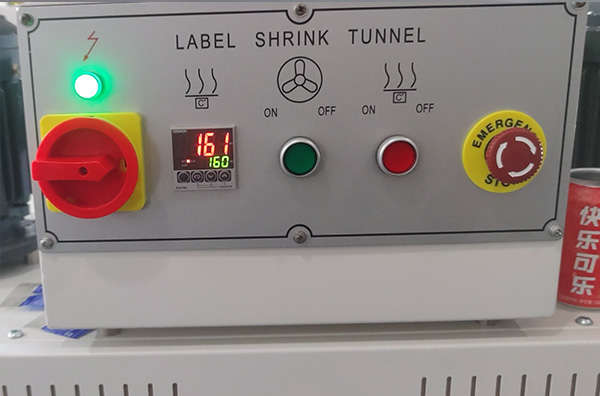
The exact temperature needed will depend on factors such as the type of material (PVC, OPS, PETG, PLA, etc.), the film’s thickness, the conveyor’s speed, and the tunnel’s specific design. It is crucial to carefully control the temperature by the material’s specifications to achieve consistent and high-quality shrinkage without damaging the product or its packaging. Always refer to the manufacturer’s guidelines or conduct thorough testing to determine the optimal temperature for your specific application.
The components of the heat shrink tunnel
Heating Element
The electric heating element is at the core of the electric heat shrink tunnel, usually comprised of electric heating wires. These wires generate uniform heat throughout the tunnel. Think of it as a controlled oven that evenly cooks your favorite dish – only in this case, it’s shrinking the shrinkable sleeve label around your product.
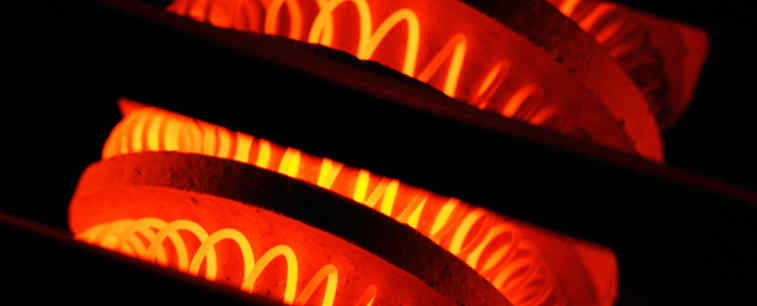
Conveyor System
When it comes to shrink wrapping, the conveyor isn’t just a part of the process; it’s the heart that smoothly carries your product from the beginning to the end of its shrink-wrapped journey. Think of it as a carefully guided tour, where the conveyor’s speed, style, and structure are tailored to your product’s unique needs.
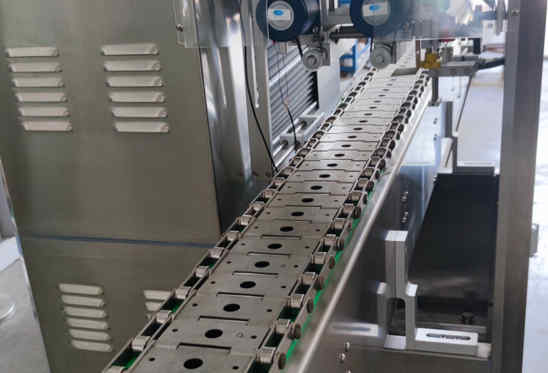
Adjustable Speed: The conveyor’s speed can be fine-tuned, controlling how long your product stays in the heat. It’s about giving each item the right amount of time to shrink to perfection, whether moving at a slow crawl or several feet per minute.
Conveyor Styles: Picking the suitable conveyor is like choosing the right pair of shoes; it must fit the product. Each style has perks, from ordinary and strong steel wire mesh to the stainless steel chain plate conveyor. Even the roller conveyors have their place, especially for more oversized items. It’s about finding the match for your product’s size, weight, and the nature of your shrink process.
The Right Fit: The product must fit the machine’s aperture. Some machines come with broader or narrower openings; choosing the wrong one could be a packaging faux pas. That’s why sending your product to our team can be a wise step, ensuring you get the right equipment for your specific needs.
Blower System
The blower system circulates the hot air generated by the heating element around the package. It’s like having a fan in your oven that ensures everything cooks evenly. In the shrink tunnel, the blower ensures that every part of the shrinkable material receives the right amount of heat, causing it to contract snugly around the product. Imagine wrapping your product in a warm hug – that’s what the blower does, helping to form a perfect fit.
Controlled Temperature
The hot air heat shrink tunnel doesn’t just shrink the product with heat; it’s all about precision and control. It’s like having a personal chef watching over a soufflé – the temperature needs to be just right, and the timing has to be perfect.
Temperature Regulation: Electric heat shrink tunnel has thermostats and temperature sensors that constantly monitor and regulate the heat. This ensures that the shrink sleeve gets the exact temperature, whether it’s PVC, PETG, OPS, or PLA. Each material has its unique shrinkage temperature, and the machine can be adjusted accordingly.
Air Circulation: Here’s where the blower comes in. It’s not enough to heat the air; it must be evenly distributed. The blower circulates the hot air, ensuring every inch of the product receives uniform heat. This prevents any distortion or uneven shrinkage, giving your package that perfect, glove-like fit.
Speed Control: The conveyor belt’s speed can be adjusted. Need to slow it down for a more intricate package or speed it up for a more straightforward design? You’ve got the control.
Cooling Phase: Once the package leaves the heated area of the tunnel, it moves into a cooling phase. This step is essential to set the shrink material in place, locking in that perfect form. It ensures that everything stays in the right shape and texture.
Essential Considerations Before Purchasing an Electric Shrink Tunnel
Before investing in an electric shrink tunnel, it’s crucial to thoroughly assess your production requirements and understand the machine’s functionality. Here is a comprehensive summary of the critical details that need confirmation and attention:
Opening Size and Width: Assess the required size of the opening, including its width, based on the size of the products you plan to package. Consider both regular and irregular shapes.
Heating tunnel Length: Determine the appropriate length of the heating chamber to ensure optimal heating and shrinkage of the material.
Belt Speed: Identify the minimum and maximum belt speed that suits your product needs. As discussed earlier, the conveyor speed is a vital factor affecting the shrinkage quality.
Temperature Range: Confirm the minimum and maximum temperature needed for the shrinkage process to accommodate various product materials.
Chamber Type: Decide between a single or double chamber tunnel, depending on your production volume and specific needs.
Belt Type: Select the conveyor belt type that aligns with your product type, considering factors like durability, flexibility, and heat resistance.
Control Preferences: Choose between digital or analog controls based on your comfort level, functionality, and precision requirements.
Electrical Specifications: Confirm the required voltage, electrical phase, hertz, and amps to ensure compatibility with your existing infrastructure.
In Conclusion
When buying an electric heat shrink tunnel, it’s important to consider multiple factors carefully. It’s a complex decision. Understanding and confirming that these details align with your needs is essential to making an informed and effective purchase. Consulting with a professional manufacturer who can provide specialized insight and conduct product testing is a wise step in this critical investment.